Making The Instruments That Help Make The Science
Meet The Integrated Instrument Development Facility Team
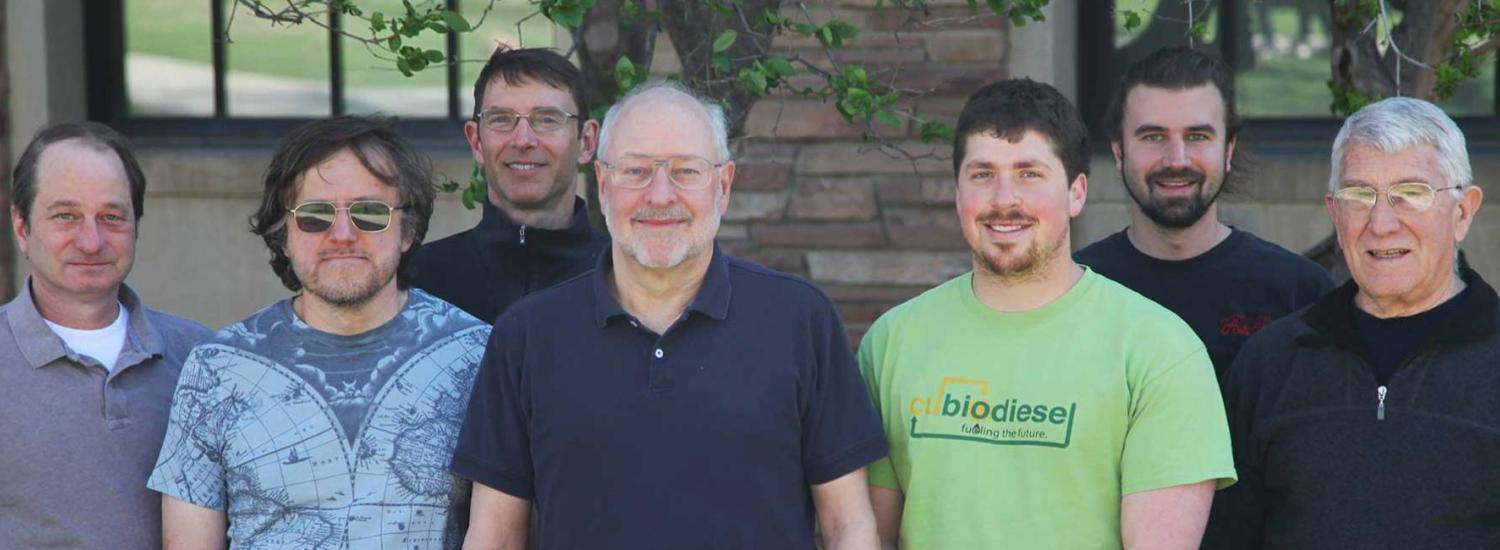
A labyrinth of hallways and doors brings you deep into the bowels of the CIRES building, to a series of rooms with almost no windows or natural light, known as the Integrated Instrument Development Facility (IIDF). “We need cameras on the roof so we can get a feed of what the weather’s like outside,” jokes Don David, the facility’s director. But despite its basement location, there’s a whole world of invention and innovation happening down in IIDF.
A group of instrument designers, glass blowers, electronics experts and machinists design, build and test scientific instruments for CIRES, the chemistry department and the wider CU Boulder community. IIDF consists of an electronics shop, a precision machining shop, a glassblowing shop, as well as lab equipment and repair. David’s been here for 19 years and he rattles off a list of groups they’ve collaborated with, including NOAA, National Institute of Standards and Technology, National Renewable Energy Laboratory, the BioServe Space Technologies Center with CU’s Aerospace Engineering and Sciences Department, and the CU physics department.
“We have a lot of materials and equipment, not to mention experience, that’s just not widely known,” he says. But for a handful of CIRES scientists that do know about them, IIDF has built some incredibly useful instruments. Among them is something called a chilled frost point hygrometer (CFH), which is an instrument attached to a balloon to measure the frost point from the troposphere to the stratosphere. David points out that it was such a useful instrument, it actually became a commercial product.
Ken Smith was the co-designer of this CFH. He’s a scientific instrument maker in the Electronics Shop and has worked at IIDF for 17 years. While different types of CFH devices have been around for a long time, Smith created an enhanced version in 2003 for then CIRES scientist Holger Voemel. Use of this instrument has become widespread, including by research groups in Europe, Japan and China. “We’re still refining and improving on it,” says Smith. “I’m really proud of it.”
Machinist Danny Warren also works in the IIDF––he started as a student employee in 2011 and stayed on after graduation, just finishing his apprenticeship at the beginning of April. “This job involves a lot of problem-solving,” he says cheerfully. “And some of the things we’re asked to make can be pretty challenging. Someone comes to us with an idea, hands us a drawing of what they want and we get to create it.”
That requires a lot of planning, thinking ahead, running through the order of operations and precision, precision, precision. The different shops––glass-blowing, machine––and offices are filled with highly advanced machines that drill and mill metals to accuracy within half the width of a strand of human hair.
Warren just finished up a project for BioServe. They had square plastic flasks with a very specific growth medium on one interior surface. That growth medium isn’t available anywhere else, but the fact that it’s inside a flask makes it hard for the BioServe scientists to use. So they asked Warren to help them get easier access, keeping in mind that the medium is extremely sensitive. After some trial and error, Warren finally milled tiny perforations in a rectangular shape on outside of the flask, using a technique that limited the damage to the growth medium. The perforations allowed the BioServe scientists to carefully cut out that side of the flask, resulting in a flat plate that they could use for their experiments. In June, via the next Space X mission, those plates will be sent to the International Space Station to see how the various cultures on them react to life in space.
Left: The full flask with perforations drilled and milled into it. Right: A prototype of the flat plate after being removed from the flask. Credit: Danny Warren/CIRES.
Another project that Ken Smith finalized recently was for CIRES Fellow Jose Luis Jimenez. His lab is gearing up to gather data on global distributions of aerosols and their chemistry, looking specifically at the interactions of Chinese and Korean pollution. They needed a power supply box and a sensor interface box––pretty simple items but they needed them quickly and to certain specifications. “We have an aircraft instrument that goes on a NASA aircraft and we needed to replace parts on that instrument and upgrade them,” says Pedro Campuzano Jost, a research scientist in the Jimenez lab. “It was something we could have done ourselves but we didn’t have the manpower and the power box is something that has to work on a hot airplane over the Pacific.”
“Pedro brought us a schematic and asked us to help make it a reality,” says Smith. “This was pretty straightforward but a lot of the fun comes from puzzling out how to turn schematic into reality. The goal is to develop a product that’s as user-friendly as possible.”
Smith has also done work for CIRES Fellow Veronica Vaida, who asked him to refurbish a 1985 enhanced spectrometer. By attaching a motor and updating the communications and code to work with modern computers and programs, Smith essentially revived an old machine that might otherwise be obsolete. He says they’ve done that with a lot of older machines and, in fact, the old machines are often better made to begin with and with a little update, can last a long time.
These projects are just a handful of the many they’ve designed and built over the years. The IIDF staff has a combined experience of over 120 years and are willing to give just about anything a try. “Don’t be afraid to ask us,” says David. “We’re here to help you get your science done––it’s our job.”